- Joined
- Dec 9, 2010
- Messages
- 29
- Motherboard
- iMac 27" (Late 2012)
- CPU
- Intel Core i7 3770 @ 3.4GHz
- Graphics
- GeForce GTX 680MX
- Mac
- Classic Mac
- Mobile Phone
Hey all,
I'm in the process of working on my Power Mac G4 Quicksilver case conversion for my main desktop rig, and I wanted to share my progress and work here. I've been inspired by a lot of the really great G5/Mac Pro mods on this forum, but I wanted to do something different and I personally prefer the older G4 case design to the newer Mac towers. Aside from that, there are very few G3/G4 chassis conversions out there, and even fewer still that didn't make me cringe at the hackery! (more on that later)
Having been a Mac user for life (the first Mac in the house was an SE running System 6) there were plenty of old Macs floating around the house to choose from. I got to eyeing my Power Mac G4 Cube, and thinking that I could pick up an empty Cube on eBay and fit it with a mini-ITX board. Unfortunately, that would require replacing my 1366 processor and almost every other component, so I quickly decided that I needed to use a case that could accommodate a micro-ATX board that would be able to use my existing CPU, RAM, and video card. I had settled on a Sawtooth G4, but that changed when my boss happened to give me the Quicksilver with a dead logic board while I was still in the planning stages! The Quicksilver was a perfect choice for me because it is still modern and sleek enough looking after all these years and the silver color scheme still nicely matches modern Apple keyboards/mice/displays. Moreover, I am a fan of small computers, and the G4 towers are about as compact as you can make a non-ITX system and are no bigger than the Antec Super LanBoy which currently houses my Hackintosh (something that can definitely not be said for the G5/Mac Pro). And so, the ultimate Power Mac G4 upgrade was started... a project I like to refer to as the Power Mac i7.
The G4 Quicksilver before starting the project:
One of my favorite features has always been the fold-down motherboard door. It makes upgrading and tinkering, both of which I do frequently, an absolute breeze. Plus, it's just slick.
The biggest problem with using this case, airflow issues aside, is the optical drive bay. Because of the position of the memory slots on a standard ATX or mATX board, they hit the optical drive carrier and prevent the door from coming even close to closing. The original Apple board was conveniently laid out to avoid this issue, but we have no such luxury with off-the-shelf parts! The optical drive carrier would literally have to be about half the length it is now, and nobody makes a standard drive of that length. This particular pesky issue actually caused me to abandon a project like this six or seven years ago without even starting, but I have some ideas to bypass it now.
The back of the computer also poses a couple of issues. For one thing, the spacing between the I/O ports and the expansions slots is way too large for a mATX board. Most of the other G4 mods I have seen skate this issue by just accepting that the thick plastic pillar will block the audio ports and adding a PCI audio card, or making ugly cuts to the plastic/metal. Naturally, these are compromises that I won't accept! The other problem is the power supply. The original part is basically an ATX PSU with some of the pins switched (thanks, Apple) so mounting it is not a problem, but finding a modern one that lines up with the fan and socket openings on the plastic is a bit of a challenge. Most modern PSUs have just a single 120mm fan on the bottom rather than a rear 80mm, and with the mounting orientation in this case, that big fan would be pressed up against the side of the chassis which would cause all sorts of problems. Fortunately, I managed to find a suitable PSU with the features that I wanted. In order to keep the mod as Apple stock as possible in appearance, it's important to me to retain as much of the original back plastic as possible rather than having the bare chassis back here, which would no doubt make things easier.
Build Specs:
Project Objectives:
So that's the introduction! I've been working on this for a month or so now and documenting as I go, so I'll be posting updates as soon as I have time to write it up. As always, feedback and ideas are welcome as you guys are pretty amazing at coming up with clever solutions to stuff.
I'm in the process of working on my Power Mac G4 Quicksilver case conversion for my main desktop rig, and I wanted to share my progress and work here. I've been inspired by a lot of the really great G5/Mac Pro mods on this forum, but I wanted to do something different and I personally prefer the older G4 case design to the newer Mac towers. Aside from that, there are very few G3/G4 chassis conversions out there, and even fewer still that didn't make me cringe at the hackery! (more on that later)
Having been a Mac user for life (the first Mac in the house was an SE running System 6) there were plenty of old Macs floating around the house to choose from. I got to eyeing my Power Mac G4 Cube, and thinking that I could pick up an empty Cube on eBay and fit it with a mini-ITX board. Unfortunately, that would require replacing my 1366 processor and almost every other component, so I quickly decided that I needed to use a case that could accommodate a micro-ATX board that would be able to use my existing CPU, RAM, and video card. I had settled on a Sawtooth G4, but that changed when my boss happened to give me the Quicksilver with a dead logic board while I was still in the planning stages! The Quicksilver was a perfect choice for me because it is still modern and sleek enough looking after all these years and the silver color scheme still nicely matches modern Apple keyboards/mice/displays. Moreover, I am a fan of small computers, and the G4 towers are about as compact as you can make a non-ITX system and are no bigger than the Antec Super LanBoy which currently houses my Hackintosh (something that can definitely not be said for the G5/Mac Pro). And so, the ultimate Power Mac G4 upgrade was started... a project I like to refer to as the Power Mac i7.
The G4 Quicksilver before starting the project:
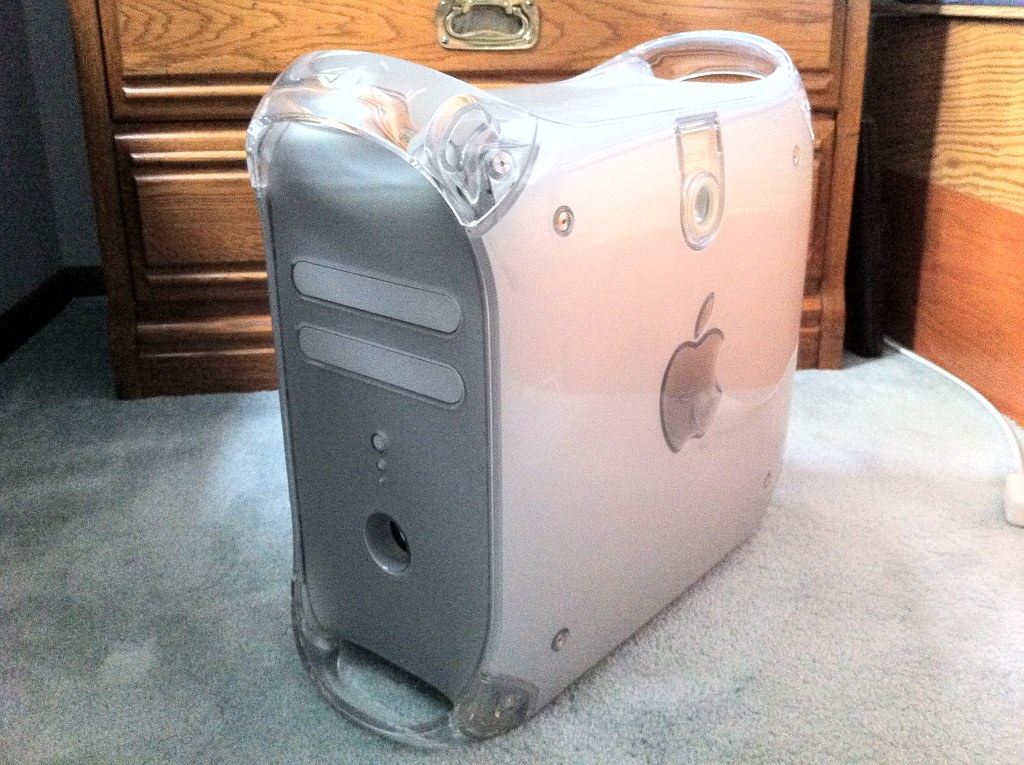
One of my favorite features has always been the fold-down motherboard door. It makes upgrading and tinkering, both of which I do frequently, an absolute breeze. Plus, it's just slick.
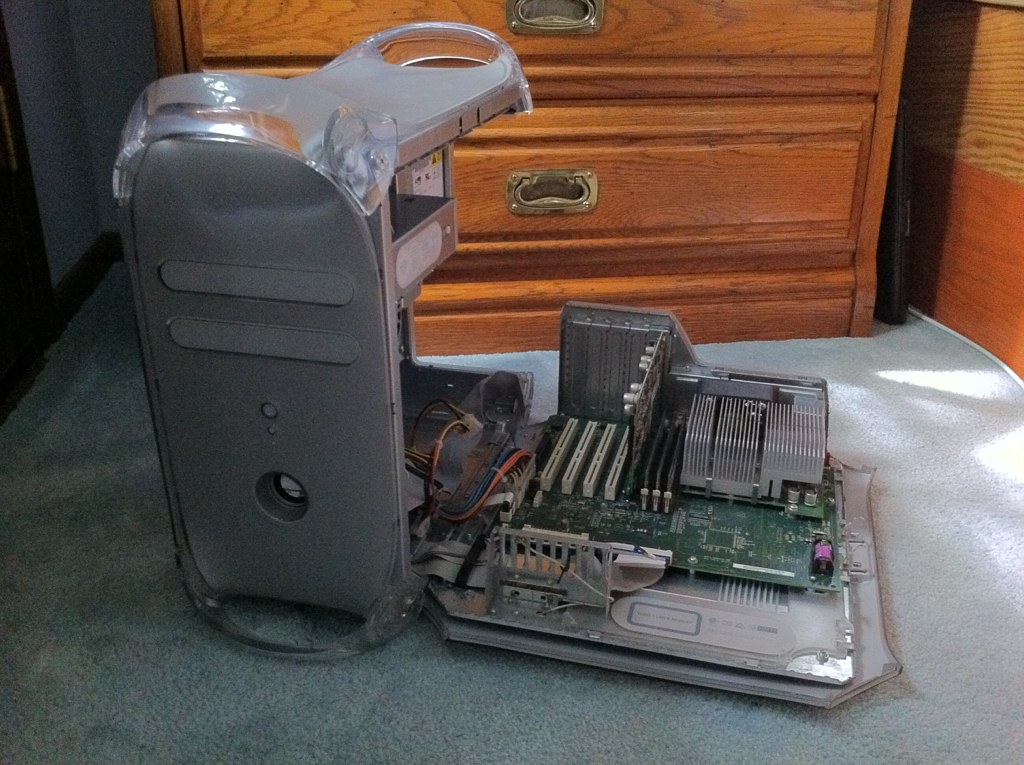
The biggest problem with using this case, airflow issues aside, is the optical drive bay. Because of the position of the memory slots on a standard ATX or mATX board, they hit the optical drive carrier and prevent the door from coming even close to closing. The original Apple board was conveniently laid out to avoid this issue, but we have no such luxury with off-the-shelf parts! The optical drive carrier would literally have to be about half the length it is now, and nobody makes a standard drive of that length. This particular pesky issue actually caused me to abandon a project like this six or seven years ago without even starting, but I have some ideas to bypass it now.
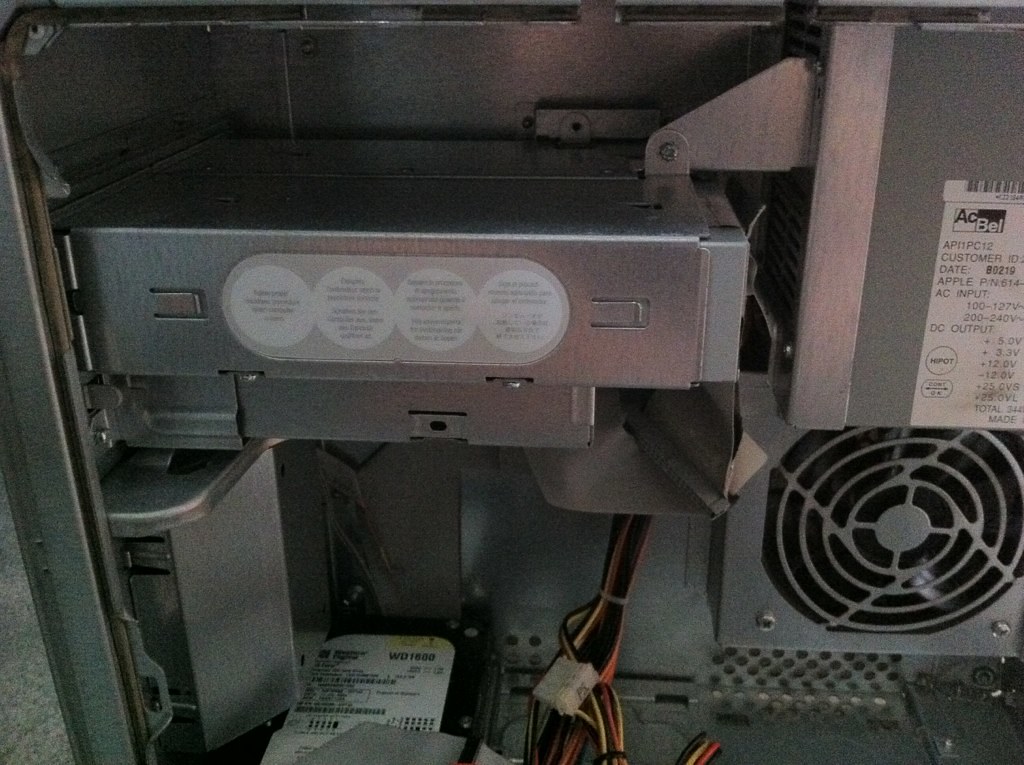
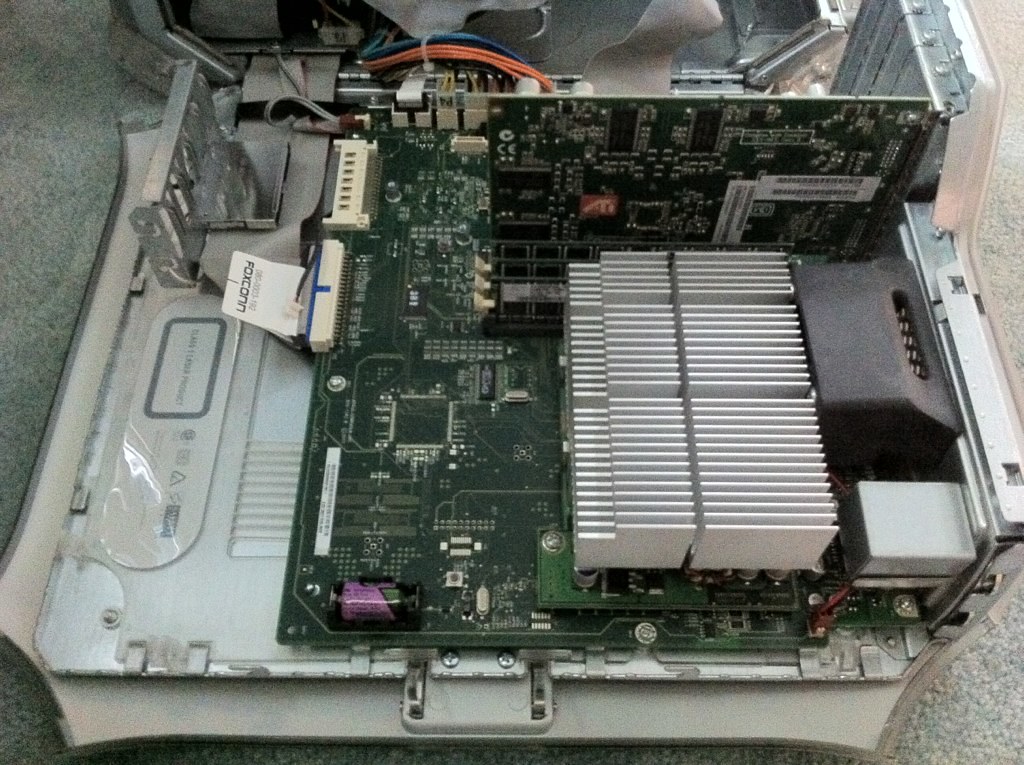
The back of the computer also poses a couple of issues. For one thing, the spacing between the I/O ports and the expansions slots is way too large for a mATX board. Most of the other G4 mods I have seen skate this issue by just accepting that the thick plastic pillar will block the audio ports and adding a PCI audio card, or making ugly cuts to the plastic/metal. Naturally, these are compromises that I won't accept! The other problem is the power supply. The original part is basically an ATX PSU with some of the pins switched (thanks, Apple) so mounting it is not a problem, but finding a modern one that lines up with the fan and socket openings on the plastic is a bit of a challenge. Most modern PSUs have just a single 120mm fan on the bottom rather than a rear 80mm, and with the mounting orientation in this case, that big fan would be pressed up against the side of the chassis which would cause all sorts of problems. Fortunately, I managed to find a suitable PSU with the features that I wanted. In order to keep the mod as Apple stock as possible in appearance, it's important to me to retain as much of the original back plastic as possible rather than having the bare chassis back here, which would no doubt make things easier.
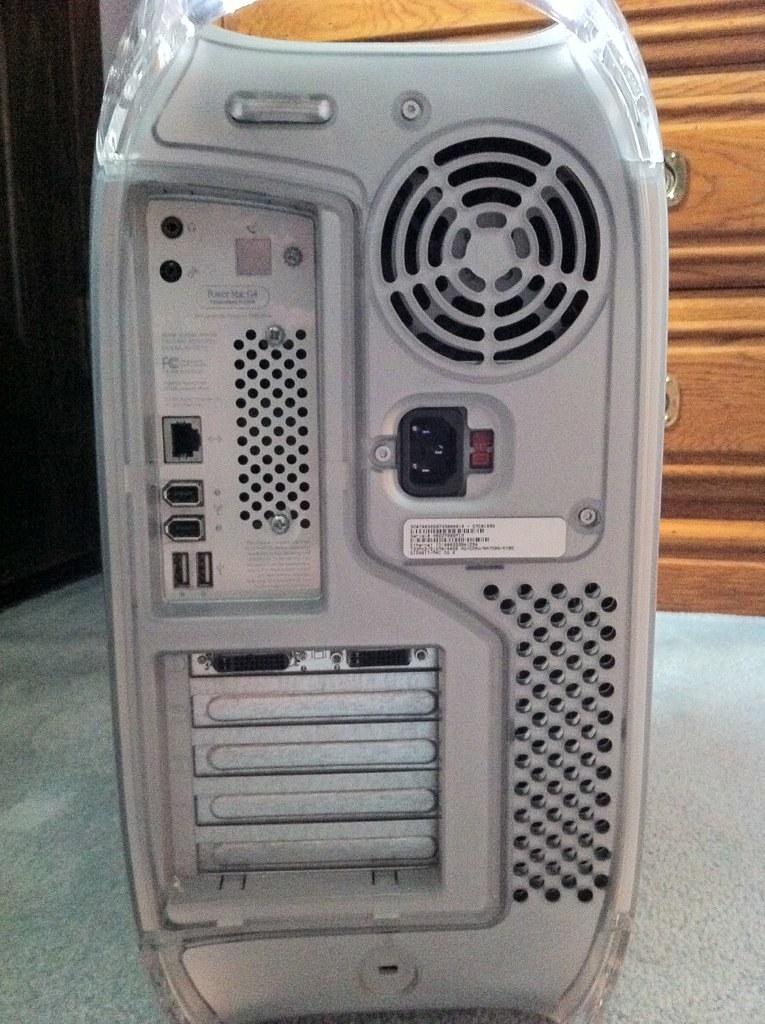
Build Specs:
- Intel Core i7 970 - 6 Cores @ 3.2GHz (LGA 1366)[/*:m:3kxx5qh6]
- ASUS Rampage II GENE (The GENE is necessary to fit the mATX requirement of the G4 case)[/*:m:3kxx5qh6]
- 24GB (6x4GB) Corsair Vengeance[/*:m:3kxx5qh6]
- XFX Radeon 5770[/*:m:3kxx5qh6]
- 2x160GB Intel 320-series SSD in RAID 0 as boot drive[/*:m:3kxx5qh6]
- 2x1TB Seagate Barracuda for storage[/*:m:3kxx5qh6]
- Of course, Mac OS X Mountain Lion[/*:m:3kxx5qh6]
Project Objectives:
- Case must appear stock from the outside. This was my biggest disappointment when researching previous G4 case mods... all but a couple that I saw look like total hackjobs. The back panels usually look sloppy, and almost all of them cut blowholes into the top of the case.[/*:m:3kxx5qh6]
- Avoid cutting visible fan holes in the case. Airflow is definitely an issue in this chassis with a modern CPU. My plan to combat this is to watercool the system, with the radiator exhausting out the bottom of the chassis where its hole is conveniently concealed from the outside.[/*:m:3kxx5qh6]
- Retain all functionality of the original Power Mac G4. A lot of the mods I have seen give up the internal optical drive in order to make everything fit. **After exploring many ways to do this, I eventually abandoned this plan. It was certainly doable, but I ultimately decided that I almost never use optical media for anything and leaving the space open gave me too many other options. A USB optical drive is in my desk drawer for the rare occasion I need to burn a disc.**[/*:m:3kxx5qh6]
- Clean look on the inside. Let's face it, a modded case is going to be opened and inspected by every enthusiast that you meet. And I'm using an Apple chassis. If it wouldn't have met Steve Jobs' approval, I don't want it in my design. This is going to make cable management extremely important.[/*:m:3kxx5qh6]
- Upgradeability. If I do things right, upgrading will be as simple as dropping a new mATX board into a regular ATX case. This is important, because I do upgrade frequently, and I don't want to have to re-mod every time I want to do this.[/*:m:3kxx5qh6]
So that's the introduction! I've been working on this for a month or so now and documenting as I go, so I'll be posting updates as soon as I have time to write it up. As always, feedback and ideas are welcome as you guys are pretty amazing at coming up with clever solutions to stuff.